The advance allows for accurate measurement of the hydrodynamic properties of synthetic shark skin, and could inspire improved swimsuit, boat, and aircraft designs

Scientists have been trying to unlock the secrets of shark skin for more than 50 years. The key to sharks’ hydrodynamic prowess lies in how the rigid, tooth-like structures that coat their flexible skin change the flow of water as sharks swim forward – but attempts to quantify this effect have fallen short. After all, it’s tough to fabricate a material that closely mimics shark skin, a marvel of Nature honed over the 400 million years that sharks have sleuthed the seas.
"Most previous studies used flat plates covered with aluminum protrusions, which didn’t account for the way sharks move," said George Lauder, Ph.D., a Harvard Biology professor who specializes in the biomechanics of aquatic locomotion in fishes. "We had a hunch that movement is a critical factor in understanding shark propulsion – so we knew our next step was to fabricate a much more realistic material with the hard structures attached to a flexible membrane."
The only way to achieve this truly bioinspired design was to use a 3D printer that had the capabilities of incorporating multiple materials into a single printed model, said Lauder, who teamed up with Wyss Institute Senior Research Scientist James Weaver, Ph.D., and Li Win, Ph.D., now at Beihang University in China, to give it a shot. Weaver, who works at the interface between zoology, materials science, and multi-material additive manufacturing, said no one had ever attempted to fabricate a structurally realistic and mechanically robust flexible shark skin mimic with a 3D printer before, but he was up to the challenge.
After a year of work, the trio fabricated the first biomimetic shark skin and quantified its hydrodynamic benefits, a salty sweet success that they reported in the Journal of Experimental Biology and was highlighted on the cover of the May, 2014 issue. The advance could eventually inspire new applications from swimsuit design to watercraft and even aircraft design.
A fabrication frenzy-turned-feat
Lauder and Win first took high-resolution x-ray scans of the skin of a mako shark from a Boston fish market. The images revealed the stunning complexity of the tooth-like structures called denticles that cover shark skin and make it feel like sandpaper in one direction.
Denticles vary in shape and size among shark species and even along the body of a single shark. In fast swimming open water species, the denticles have a stalk-like neck that anchors them to the skin of the shark, and they also overlap each other; from a side view, each denticle curves up and backward – looking a bit like the profile of a duck’s head.
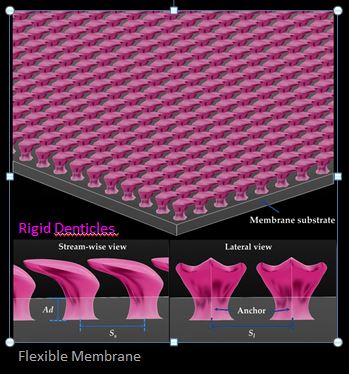
Lauder and Win selected a single representative denticle from the mako scans, and built a 3D computer model showing thousands of the same denticle laid out in rows along a flexible membrane. Then it was time for Weaver to turn the model into a shark skin replica using the state-of-the-art multi-material 3D printing capabilities at the Wyss Institute.
At first, the denticles kept breaking off, Weaver said, and it was impossible to print the denticles at their natural size (about 150 micrometers, which is about the size of a dust particle), but after months of trial and error, and continuous design and resin formulation changes, he produced a convincing shark skin sample with scaled-up denticles firmly anchored into the flexible basal membrane and showcasing enough complexity to be both realistic and highly functional.
Once the shark skin mimic was fabricated, Weaver analyzed the material using scanning electron microscopy, confirming that the fabrication process was a success, and that all of the critical fine-scale structurally details of the native denticles had been faithfully replicated.
Next it was time to test the shark skin sample against a smooth, denticle-less sample in Lauder’s flow tank, which he calls his fish treadmill. A robotic flapping device controls the various hydrodynamic conditions of the tank, such as flow speed and direction.
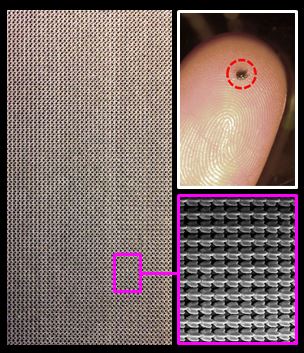
One key result confirmed Lauder’s hunch about the importance of shark movement in these hydrodynamic studies: when in a static position, the biomimetic shark skin reduced drag (fluid resistance) compared to the smooth membrane at slower flow speeds, but actually increased drag at higher speeds. However, when the team moved the robotic flapping device, which was coated with the synthetic shark skin, to mimic the way a shark moves, the performance of the shark skin improved significantly. Compared to a smooth control membrane, the flexible biomimetic shark skin increased swimming speed by more than six percent, and reduced the energy it takes to swim by approximately the same amount.
The shark skin membrane also generated a more robust vortex of water along its leading edge – which may also confer an additional swimming advantage to sharks, Lauder said. "These eddies sort of help to suck the shark forward as it swims," he said, asserting the need to further investigate thrust generation in addition to drag reduction.
Next, the team would like to change the denticle pattern on the membrane, including the spaces between the denticles, to see how that affects swimming efficiency. "What we know for sure is that denticles are complex structures and exhibit incredibly high structural diversity amongst different shark species," Weaver said. "For example, fast-swimming open ocean species have denticles that are radically different from their slow-moving counterparts that spend their time on the sea floor."
This work was funded by the Wyss Institute and the National Science Foundation.