Researchers create ultra slippery anti-ice and anti-frost surfaces
A team of researchers from Harvard University have invented a way to keep any metal surface free of ice and frost. The treated surfaces quickly shed even tiny, incipient condensation droplets or frost simply through gravity. The technology prevents ice sheets from developing on surfaces — and any ice that does form, slides off effortlessly.
The discovery, published online as a just-accepted-manuscript in ACS Nano on June 10, has direct implications for a wide variety of metal surfaces such as those used in refrigeration systems, wind turbines, aircraft, marine vessels, and the construction industry.
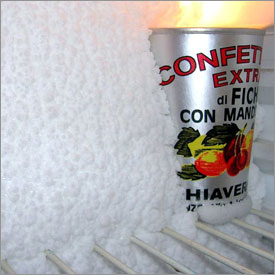
The group, led by Joanna Aizenberg, Amy Smith Berylson Professor of Materials Science at the Harvard School of Engineering and Applied Sciences (SEAS) and a Core Faculty Member at the Wyss Institute for Biologically Inspired Engineering at Harvard, previously introduced the idea that it was possible to create a surface that completely prevented icewith ice-repellent coatings, inspired by the water repellent lotus leaf. Yet this technique can fail under high humidity as the surface textures become coated with condensation and frost.
“The lack of any practical way to eliminate the intrinsic defects and inhomogeneities that contribute to liquid condensation, pinning, freezing, and strong adhesion, have raised the question of whether any solid surface (irrespective of its topography or treatment) can ever be truly ice-preventive, especially at high-humidity, frost-forming conditions,” Aizenberg said.
To combat this problem, the researchers recently invented a radically different technology that is suited for both high humidity and extreme pressure, called SLIPS (Slippery Liquid Infused Porous Surfaces). SLIPS are designed to expose a defect-free, molecularly flat liquid interface, immobilized by a hidden nanostructured solid. On these ultra smooth slippery surfaces fluids and solids alike — including water drops, condensation, frost, and even solid ice—can slide off easily.
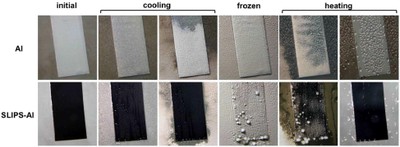
The challenge was to apply this technology to metal surfaces, especially as these materials are ubiquitous in our modern world, from airplane wings to railings. Aizenberg and her team developed a way to coat the metal with a rough material that the lubricant can adhere to. The coating can be finely sculpted to lock in the lubricant and can be applied over a large scale, on arbitrarily shaped metal surfaces. In addition, the coating is non-toxic and anti-corrosive.
To demonstrate the robustness of the technology, the researchers successfully applied it to refrigerator cooling fins and tested it under a prolonged, deep freeze condition. Compared to existing “frost-free” cooling systems, their innovation completely prevented frost far more efficiently and for a longer time.
“Unlike lotus leaf-inspired icephobic surfaces, which fail under high humidity conditions, SLIPS-based icephobic materials, as our results suggest, can completely prevent ice formation at temperatures slightly below 0*C while dramatically reducing ice accumulation and adhesion under deep freezing, frost-forming conditions,” said Aizenberg.
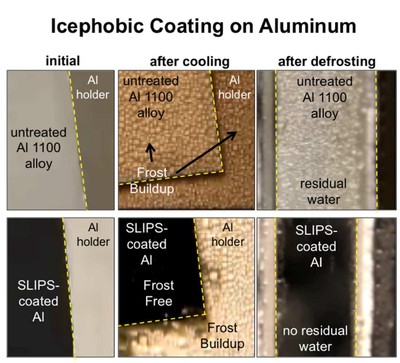
In addition to allowing for the efficient removal of ice, the technology lowers the energy costs associated by several orders of magnitude. Thus, the readily scalable approach to slippery metallic surfaces holds great promise for broad application in the refrigeration and aviation industry and in other high-humidity environments where an icephobic surface is desirable.
For example, once their technology is applied to a surface, ice on roofs, wires, outdoor signs, and wind turbinescould be easily removed merely by tilting, slight agitation, or even wind and vibrations.
“This new approach to icephobic materials is a truly disruptive idea that offers a way to make a transformative impact on energy and safety costs associated with ice, and we are actively working with the refrigeration and aviation industries to bring it to market,” said Aizenberg.
Aizenberg is also Professor of Chemistry and Chemical Biology in the Department of Chemistry and Chemical Biology, and Susan S. and Kenneth L. Wallach Professor at the Radcliffe Institute for Advanced Study, and Director of the Kavli Institute for Bionano Science and Technology at Harvard. Her co-authors included Philseok Kim, a Technology Development Fellow at the Wyss Institute and SEAS; Tak-Sing Wong of the Wyss Institute and SEAS; Jack Alvarenga of the Wyss Institute; Michael J. Kreder of the Wyss Institute; and Wilmer E. Adorno-Martinez of University of Puerto Rico.
The authors received support from the Materials Research Science and Engineering Center (MRSEC) at Harvard under NSF award #DMR-1005022. The Wyss Institute at Harvard University also provided support for this work. Part of this work was performed at the Center for Nanoscale Systems (CNS) at Harvard supported under NSF award #ECS-0335765. In addition, the team acknowledges the Croucher Foundation Postdoctoral Fellowship; the REU BRIDGE, co-funded by the ASSUREprogram of the DoD in partnership with the NSF REU Site program under NSF Grant #DMR-1005022.